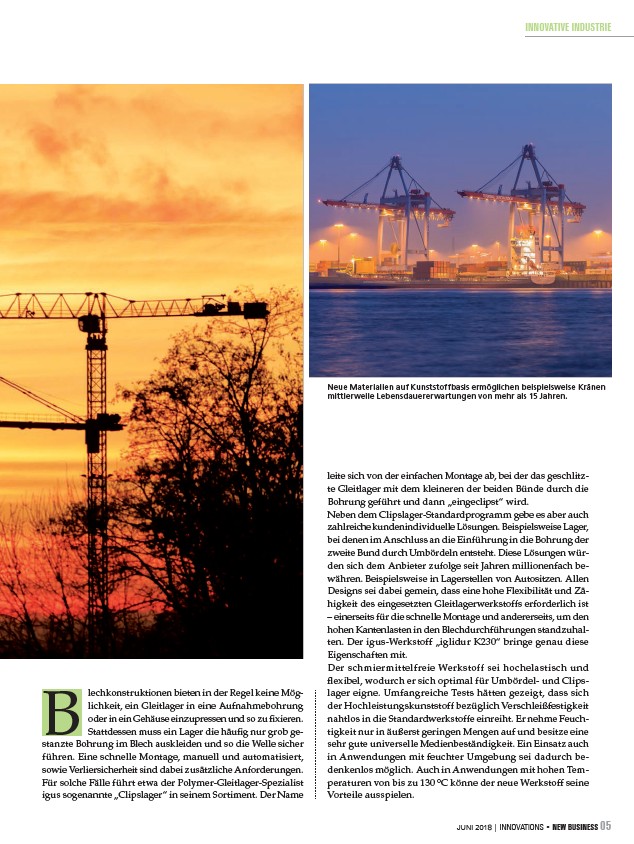
INNOVATIVE INDUSTRIE
Neue Materialien auf Kunststoffbasis ermöglichen beispielsweise Kränen
mittlerweile Lebensdauererwartungen von mehr als 15 Jahren.
JUNI 2018 | INNOVATIONS • NEW BUSINESS 05
Blechkonstruktionen bieten in der Regel keine Möglichkeit,
ein Gleitlager in eine Aufnahmebohrung
oder in ein Gehäuse einzupressen und so zu xieren.
Stattdessen muss ein Lager die häu g nur grob gestanzte
Bohrung im Blech auskleiden und so die Welle sicher
führen. Eine schnelle Montage, manuell und automatisiert,
sowie Verliersicherheit sind dabei zusätzliche Anforderungen.
Für solche Fälle führt etwa der Polymer-Gleitlager-Spezialist
igus sogenannte „Clipslager“ in seinem Sortiment. Der Name
leite sich von der einfachen Montage ab, bei der das geschlitzte
Gleitlager mit dem kleineren der beiden Bünde durch die
Bohrung geführt und dann „eingeclipst“ wird.
Neben dem Clipslager-Standardprogramm gebe es aber auch
zahlreiche kundenindividuelle Lösungen. Beispielsweise Lager,
bei denen im Anschluss an die Einführung in die Bohrung der
zweite Bund durch Umbördeln entsteht. Diese Lösungen würden
sich dem Anbieter zufolge seit Jahren millionenfach bewähren.
Beispielsweise in Lagerstellen von Autositzen. Allen
Designs sei dabei gemein, dass eine hohe Flexibilität und Zähigkeit
des eingesetzten Gleitlagerwerkstoffs erforderlich ist
– einerseits für die schnelle Montage und andererseits, um den
hohen Kantenlasten in den Blechdurchführungen standzuhalten.
Der igus-Werkstoff „iglidur K230“ bringe genau diese
Eigenschaften mit.
Der schmiermittelfreie Werkstoff sei hochelastisch und
exibel, wodurch er sich optimal für Umbördel- und Clipslager
eigne. Umfangreiche Tests hätten gezeigt, dass sich
der Hochleistungskunststoff bezüglich Verschleißfestigkeit
nahtlos in die Standardwerkstoffe einreiht. Er nehme Feuchtigkeit
nur in äußerst geringen Mengen auf und besitze eine
sehr gute universelle Medienbeständigkeit. Ein Einsatz auch
in Anwendungen mit feuchter Umgebung sei dadurch bedenkenlos
möglich. Auch in Anwendungen mit hohen Temperaturen
von bis zu 130°C könne der neue Werkstoff seine
Vorteile ausspielen.