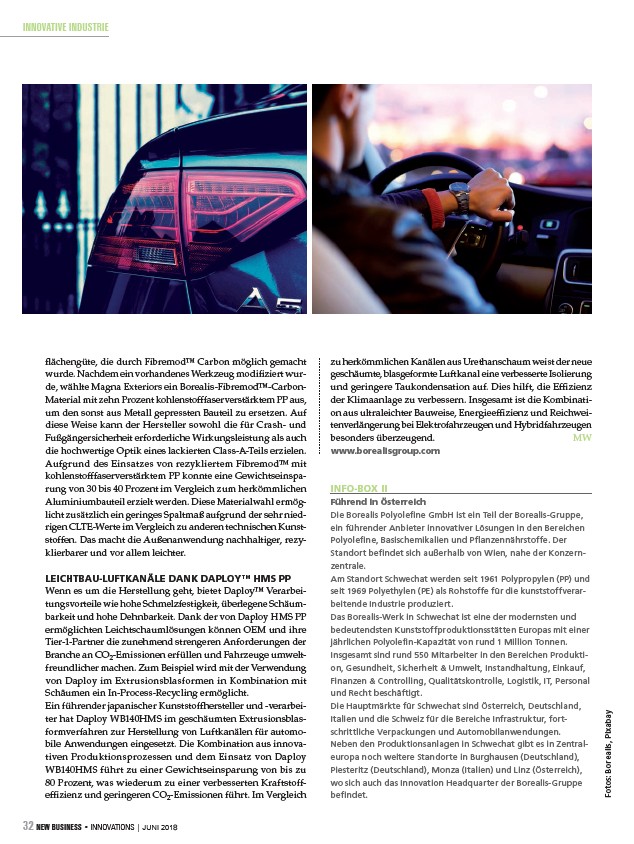
INNOVATIVE INDUSTRIE
32 NEW BUSINESS • INNOVATIONS | JUNI 2018
Fotos: Borealis, Pixabay
ächengüte, die durch Fibremod™ Carbon möglich gemacht
wurde. Nachdem ein vorhandenes Werkzeug modi ziert wurde,
wählte Magna Exteriors ein Borealis-Fibremod™-Carbon-
Material mit zehn Prozent kohlenstofffaserverstärktem PP aus,
um den sonst aus Metall gepressten Bauteil zu ersetzen. Auf
diese Weise kann der Hersteller sowohl die für Crash- und
Fußgängersicherheit erforderliche Wirkungsleistung als auch
die hochwertige Optik eines lackierten Class-A-Teils erzielen.
Aufgrund des Einsatzes von rezykliertem Fibremod™ mit
kohlenstofffaserverstärktem PP konnte eine Gewichtseinsparung
von 30 bis 40 Prozent im Vergleich zum herkömmlichen
Aluminiumbauteil erzielt werden. Diese Materialwahl ermöglicht
zusätzlich ein geringes Spaltmaß aufgrund der sehr niedrigen
CLTE-Werte im Vergleich zu anderen technischen Kunststoffen.
Das macht die Außenanwendung nachhaltiger, rezyklierbarer
und vor allem leichter.
LEICHTBAU-LUFTKANÄLE DANK DAPLOY™ HMS PP
Wenn es um die Herstellung geht, bietet Daploy™ Verarbeitungsvorteile
wie hohe Schmelzfestigkeit, überlegene Schäumbarkeit
und hohe Dehnbarkeit. Dank der von Daploy HMS PP
ermöglichten Leichtschaumlösungen können OEM und ihre
Tier-1-Partner die zunehmend strengeren Anforderungen der
Branche an CO2-Emissionen erfüllen und Fahrzeuge umweltfreundlicher
machen. Zum Beispiel wird mit der Verwendung
von Daploy im Extrusionsblasformen in Kombination mit
Schäumen ein In-Process-Recycling ermöglicht.
Ein führender japanischer Kunststoffhersteller und -verarbeiter
hat Daploy WB140HMS im geschäumten Extrusionsblasformverfahren
zur Herstellung von Luftkanälen für automobile
Anwendungen eingesetzt. Die Kombination aus innovativen
Produktionsprozessen und dem Einsatz von Daploy
WB140HMS führt zu einer Gewichtseinsparung von bis zu
80Prozent, was wiederum zu einer verbesserten Kraftstoffef
zienz und geringeren CO2-Emissionen führt. Im Vergleich
zu herkömmlichen Kanälen aus Urethanschaum weist der neue
geschäumte, blasgeformte Luftkanal eine verbesserte Isolierung
und geringere Taukondensation auf. Dies hilft, die Ef zienz
der Klimaanlage zu verbessern. Insgesamt ist die Kombination
aus ultraleichter Bauweise, Energieef zienz und Reichweitenverlängerung
bei Elektrofahrzeugen und Hybridfahrzeugen
besonders überzeugend. MW
www.borealisgroup.com
INFO-BOX II
Führend in Österreich
Die Borealis Polyolefi ne GmbH ist ein Teil der Borealis-Gruppe,
ein führender Anbieter innovativer Lösungen in den Bereichen
Polyolefi ne, Basischemikalien und Pfl anzennährstoffe. Der
Standort befi ndet sich außerhalb von Wien, nahe der Konzernzentrale.
Am Standort Schwechat werden seit 1961 Polypropylen (PP) und
seit 1969 Polyethylen (PE) als Rohstoffe für die kunststoffverarbeitende
Industrie produziert.
Das Borealis-Werk in Schwechat ist eine der modernsten und
bedeutendsten Kunststoffproduktionsstätten Europas mit einer
jährlichen Polyolefi n-Kapazität von rund 1 Million Tonnen.
Insgesamt sind rund 550 Mitarbeiter in den Bereichen Produktion,
Gesundheit, Sicherheit & Umwelt, Instandhaltung, Einkauf,
Finanzen & Controlling, Qualitätskontrolle, Logistik, IT, Personal
und Recht beschäftigt.
Die Hauptmärkte für Schwechat sind Österreich, Deutschland,
Italien und die Schweiz für die Bereiche Infrastruktur, fortschrittliche
Verpackungen und Automobilanwendungen.
Neben den Produktionsanlagen in Schwechat gibt es in Zentraleuropa
noch weitere Standorte in Burghausen (Deutschland),
Piesteritz (Deutschland), Monza (Italien) und Linz (Österreich),
wo sich auch das Innovation Headquarter der Borealis-Gruppe
befi ndet.